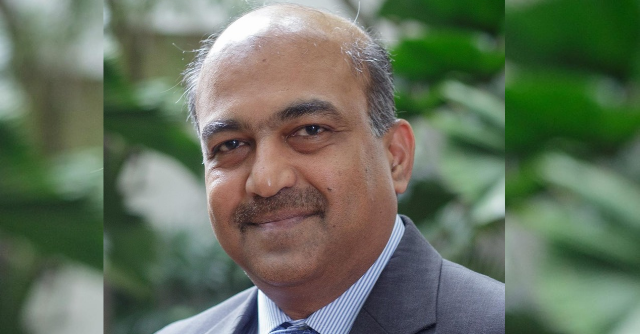
New Delhi, May 5 -- India is projected to become the world's third largest economy by 2027, with industrial production rising by 4.8% year-on-year. However, this impressive growth trajectory faces new challenges in an increasingly volatile global marketplace. Take India's commodities sector - when palm oil supplies tightened in December 2024, companies had to rapidly pivot to South American soybean oil, requiring complex shifts in sourcing, logistics, and inventory management. This kind of sudden market disruption is becoming commonplace across all industries.
For Indian industrial companies to maintain their competitive edge, traditional operating models are no longer sufficient. Today's industrial landscape demands real-time responsiveness, predictive capabilities, and seamless coordination across supply chains.
The solution lies in leveraging digitalisation for supply chain optimisation, automation, and predictive analytics, and the potential impact for India is huge. Companies that invest just 3% of their sales in digital technologies are significantly outperforming their peers, yet only 54% of Indian companies have begun adopting advanced analytics and AI. This technology gap represents sustainable growth.
Three Technologies Transforming Threats into Opportunities
For companies looking to remain competitive, build resilience, and improve their sustainability, three transformative technologies are proving to be game-changers: ecosystem-wide industrial intelligence, digital twins, and artificial intelligence (AI). Together, these solutions help companies convert challenges into strategic opportunities while building lasting competitive advantages that can weather market volatility.
Built around the integrated digital twin and overlaid with AI, a connected industrial ecosystem delivers tangible benefits to all members of the value network. By bringing together data from across the industrial lifecycle, these trusted applications drive meaningful insights and efficiency. With the cloud enabling the viewing of this integrated data in context and from anywhere, teams can collaborate and operate from a common reference point. This gives them the confidence to make decisions quickly.
This is where the second transformative application comes in; digital twins can serve as a common reference point. Defined as a virtual representation of a physical asset or process, it serves as the single source of truth for stakeholders at every step of the product or process lifecycle. Along with predictive analysis, the third component, digital twins can be used to forecast potential maintenance issues, find ways to use fewer resources, and can even be used to tackle the skills shortage by way of virtual training, optimised workflows, and remote maintenance.
Bringing industrial and generative AI technologies together strengthens these digital capabilities. This combination supports optioneering, predicts maintenance, and optimises operations in real time. The result is a perpetual state of iterative improvement arising from the use of automated processes.
Extending these benefits to the entire value chain-internally, such as across a company's distributed geographical network, or externally, including partners, suppliers and other stakeholders-builds a set of continuous feedback loops that encourage innovation. Data-powered AI networks can greatly boost the development of Industry 5.0, contributing to a more sustainable environment through resource optimisation, reduced downtime and increased adaptability. This then results in cost savings and fosters a more agile workforce.
How digital insight is delivering for profit and planet
Industrial players are already seeing significant results from the use of these technologies. Dr. Reddy's Laboratories' (DRL), a leading multinational pharmaceutical company, adopted the PI system for advanced data management at their smart manufacturing facility. It contributed to a nearly 90% increase in productivity and a 40% reduction in quality-related expenses at its flagship site. The PI System is also aligned with the group's ambitions to optimise energy use, reduce emissions and become 100% paperless by 2030.
And we're not just limited to industrial companies. For example, Namchi Smart City developed an Integrated Cross-city Command Centre and technology platform to optimise municipality services through smart technology. This resulted in energy savings of approximately 20%, through the use of devices such as automated streetlights and buildings with integrated set points and controls.
These are just a few ways that industrial businesses and governments are now making the most of digital insights to deliver for profit, people and the planet.
Industrial intelligence to thrive amid disruption and fragmentation
Research shows 84% of companies globally are making decisions with incomplete data. Yet, almost as many-78%-know that enabling data sharing drives the highest value.
Combining data analytics, AI and human creativity unlocks the industrial intelligence needed to thrive amid the threats of constant disruption and fragmentation, and with it, to create new and sustainable opportunities for the future.
As we advance towards Industry 5.0, industry intelligence is pivotal for Indian companies to navigate this transformation. By integrating real-time data and insights, businesses can anticipate market trends, optimise operations, and build more resilient models. This data-driven approach not only addresses current challenges but also positions companies to lead in this competitive landscape by aligning with global standards and ensuring sustainable growth.
Published by HT Digital Content Services with permission from TechCircle.