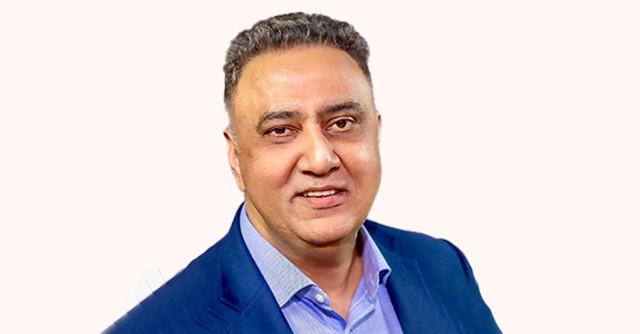
New Delhi, July 22 -- India's manufacturing sector is at a turning point as startups in electric vehicles, robotics, and clean tech push for faster, more agile product development. These companies are moving away from traditional, siloed processes and adopting integrated digital tools to manage everything from design to production. The shift is being driven not just by speed and cost pressures, but also by the need to scale quickly with limited resources. Autodesk, a global design and engineering software provider, is closely involved in this transition.
In a conversation with TechCircle, Parminder Singh, Country Head for Design & Manufacturing and Media & Entertainment, India & SAARC at Autodesk, outlines how Indian manufacturers are adapting to cloud-native and AI-driven workflows, and what it means for the next phase of industrial growth.
Edited Excerpts:
How are Indian manufacturers, especially in EVs and smart devices, changing their approach to product development?
Startups in India, especially in electric vehicles, robotics, clean tech, and consumer durables, are growing rapidly. A major challenge they face is building early-stage prototypes and understanding not just what the final product will look like, but how it will function. They also need to determine whether they can manufacture the product at scale, or if they'll need to revisit their designs later in the cycle. This process is both complex and costly.
Startups tend to move in small, agile steps, from design to other phases of product development. To support this, many are turning to integrated platforms that can handle the entire product lifecycle: from concept and engineering to validation, manufacturing, and plant design.
Tools like the Fusion platform are being adopted because they offer a single environment to manage these stages efficiently. We're seeing this shift across the board, from small EV startups to those working in consumer durables.
What role does software play in mechanical areas like prototyping, testing, or production planning?
Software is fundamental to product design. When designing a product, it's important to visualize it in three dimensions, how it will look, function, be assembled and disassembled, and how it will be serviced. These considerations must be addressed early in the design stage. A platform like Fusion enables users to design products in 3D and test them virtually under various conditions such as stress, strain, impact, and temperature, before any physical part is made.
This covers only the design phase. Once a product is designed, the data often needs to be shared with vendors or collaborators, especially in startups. These interactions may lead to design changes, which must also be reflected in the system. Fusion supports this process.
After finalizing the design, manufacturing begins, either in-house or outsourced. The same design data can be used to create tooling for production. In this way, software like Fusion supports the entire product development cycle, from design to manufacturing.
What are the top two or three structural barriers holding Indian B2B product companies back in digital manufacturing?
The first major barrier in digital manufacturing is the use of fragmented tools across different departments. Each team often uses its own software, leading to poor integration and weak collaboration. This causes inefficiencies and errors.
The second issue is overreliance on individual experience rather than using real-time data or exploring newer, more effective options. For example, when designing a factory, there are multiple ways to meet a required takt time. This could involve rearranging assembly areas or using AGVs to improve flow. But these alternatives need to be simulated and validated. Relying only on past experience without testing can lead to mistakes, cost overruns, and rework.
The third challenge is that many organizations focus either on the product or the plant, but not both together. True digital manufacturing requires integration of product, plant, and processes on a single platform to accurately simulate and plan operations.
Do you think the main barrier to adopting new technology in manufacturing is cost, complexity, skill gaps, or resistance to changing legacy systems?
In our industry, major shifts in technology tend to happen roughly every 10 years. These changes significantly impact how products are designed. One key issue is the growing skills gap, especially in industrial machinery. Our recent research shows a 160% increase in the skills shortage compared to last year. At the same time, companies in this sector are starting to use AI to support sustainability efforts.
Skills aren't the only challenge. Long project timelines and high implementation costs are also major concerns. It's not uncommon for a single project to take two to three years to complete, which slows down progress. Another challenge is the ability to adapt to change. When we work with customers, we focus on understanding their goals and constraints. Based on that, we suggest solutions that fit their specific needs.
We aim to make technology accessible, not just to large enterprises, but also to SMEs and startups. That includes providing advanced tools at a manageable cost. This is where Fusion comes in. Traditional software can take one to two years to implement. Fusion, being cloud-based, typically takes only two to three months. Customers can start using it and seeing value much faster.
How are companies using AI in design workflows while addressing data security, IP ownership, and trust in algorithmic recommendations?
AI is being explored across many functions in organizations, not just in design. In manufacturing, we're seeing companies run small-scale projects to understand how AI can support their work.
Some areas where customers are experimenting with generative AI include parts consolidation, combining multiple components into a single part, which AI can do much faster than manual methods. Another use case is evaluating components with different materials, which typically involves time-consuming analysis. AI helps speed up that process.
In design, AI is also being used to automate tool path generation. When designs change, AI can update tool paths with minimal rework. Additionally, AI is helping automate drawing generation, which remains important in India, where 2D drawings are still widely used despite the push toward 3D models.
We're also supporting customers with sketch constraints to reduce design errors. On the cloud side, we're focused on meeting security requirements. Autodesk has dedicated resources, including a security officer, to ensure compliance with customer expectations. Compared to a few years ago, there's more willingness from customers to explore AI. When we explain how data is managed, the response has generally been positive.
As design tools move to cloud-native and AI-driven environments, what major shift do you see in how Indian companies will approach product development in the next 2-3 years? Or will it take longer?
The manufacturing industry currently contributes about 14 to 15 percent of India's GDP. By 2047, the goal is to increase this to around 25 percent. The sector is evolving rapidly, especially in India. Whether in large organizations or MSMEs, companies are actively exploring new technologies, concepts, and projects.
This shift is visible across the board. At Autodesk, we're seeing both large enterprises and smaller, more agile firms adopting new technologies. Smaller companies and startups, in particular, are leveraging tools like AI and cloud computing to compensate for limited manpower. These technologies allow them to match the capabilities of larger teams.
For example, when designing a product or component, each part has specific boundary conditions and volume constraints. Using AI, companies can generate a wide range of design options by exploring different permutations. Despite having only a few key performance indicators, such as cost, sustainability, or production feasibility, startups can input these parameters and quickly narrow down to an optimal design that meets their requirements.
Published by HT Digital Content Services with permission from TechCircle.