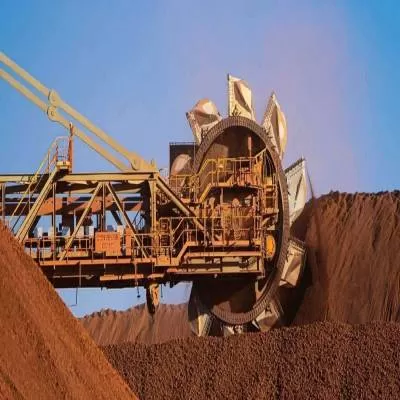
Mumbai, April 11 -- The global mining industry is undergoing a transformative shift, steered by sustainability imperatives, rising operational costs, and a pressing demand for efficiency. At the heart of this evolution lies the remanufacturing of mining components-an increasingly sought-after strategy enabling companies to extend equipment life, reduce carbon emissions, and lower capital expenditure, all while maintaining performance.
Valued at US$ 4.8 billion in 2024, the global mining remanufacturing component market is projected to grow at a CAGR of 5.5%, reaching US$ 7.1 billion by 2031. This trajectory reflects an industry-wide movement towards sustainable, cost-effective solutions-especially in the context of heavy-duty surface and underground mining operations, where downtime and equipment costs can be substantial.
Remanufacturing: A Strategic Alternative to New Equipment Mining operations place extraordinary stress on machinery, leading to frequent wear, breakdowns, and the replacement of key components. Traditionally, the sector has leaned on new parts to maintain uptime-an approach that is both costly and environmentally intensive. Remanufacturing offers a smarter path forward: components such as engines, gearboxes, axles, and hydraulic cylinders are restored to as-new condition using rigorous industrial processes and modern precision technologies.
With advancements in automation, quality assurance, and digital diagnostics, today's remanufactured components deliver performance and durability on par with original parts-at a significantly lower cost. Increasingly, mining operators are embracing this solution to meet both operational targets and environmental, social and governance (ESG) objectives.
Industry Collaboration and the Rise of the Circular Economy The market is witnessing a notable trend: major mining companies are forming partnerships with OEMs and specialist remanufacturers to establish closed-loop supply chains. These collaborations are designed to ensure the continuous reuse, restoration, and enhancement of high-value components, firmly aligning with circular economy principles.
Key Drivers of Market Growth Several converging dynamics are accelerating the uptake of remanufactured components in mining:
Cost Efficiency: Offering savings of 40-60% compared to new parts, remanufacturing is particularly appealing in times of financial constraint or global uncertainty.
Supply Chain Resilience: With global disruptions affecting part availability, local and regional remanufacturing offers shorter lead times and reduced inventory risk.
Environmental Benefits: Remanufacturing consumes up to 85% less energy than producing new components, contributing to emission reduction and waste minimisation.
Technological Enhancements: Innovations in robotics, 3D printing, and remote condition monitoring are boosting the quality, reliability, and acceptance of remanufactured parts.
Regions with strong mining activity-such as North America, Latin America, Australia, and parts of Asia-Pacific-are proving fertile ground for market expansion, particularly as operators seek to meet environmental standards without compromising output
Published by HT Digital Content Services with permission from Construction World.